MTW Milling Machine
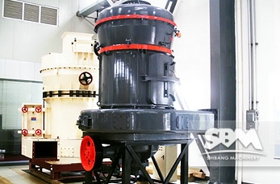
MTW Milling Machine is designed by our experienced engineers, which adopts high quality materials and advanced technology. MTW Milling Machine can meet customers' 200-33μm (80-425Mesh) powder production requirement excellently. This efficient mill has brought them enormous benefits, all of our old and new customers spoke highly of our products and service.
+86-21-58386189
+86-21-58386211
-
Low production cost, high-performance
This mill adopted bevel gear integral transmission technology. The structure is more compact, installation and adjustment are more convenient, so the efficiency is greatly increased.
-
Good stability, high reliability
Surface-type wind tunnel, which is conducive to the dispersion of the material and is not easy to block material. Shovel blade is made of high wear-resistant alloy materials, long service time.
-
Good products size composition
Adopted isolation structure between inner tube with mixed powder, and it can greatly improve the efficiency and accuracy of the powder.
The bevel gear transmits in a whole and drives the main shaft, who is connected with the roller hanger in the top. There are grinding rollers installed in the hangers and forming a swing support. The rollers rotate not just around the main shaft, but also around the grinding ring, besides, rollers can rotate to itself as well because of friction. Shovels are installed at the bottom end of hanger; when shovels rotate together with rollers, materials will be fed into space between rollers and ring to form a material layer, which will be grinded due to centrifugal force. The classifier drives the blades in the rotary table through the speed motor to classify the powder.
Name & Model | MTW110 | MTW138 | MTW175 | MTW215 | |
Ring Roller Number(pcs) | 4 | 4 | 5 | 5 | |
Major diameter of roller(mm) | Ф360×190 | Ф460×240 | Ф520×280 | Ф640x 320 | |
Inner diameter of roller (mm) | Ф1100×190 | Ф1380×240 | Φ1750×280 | Φ2150x 320 | |
Revolving Speed(rmin) | 120 | 96 | 75 | 65 | |
Revolving Speed(rmin) | <30 | <35 | <40 | <50 | |
Final size(mm) | 1.6-0.045, fineness can reach to 0.038 | 1.6-0.045, fineness can reach to 0.038 | 1.6-0.045, fineness can reach to 0.038 | 1.6-0.075, fineness can reach to 0.038 | |
Capacity(th) | 3.5-10 | 6.5-15 | 13-20 | 30-45 | |
Overall dimension(mm) | 8625×7933×8642 | 10920×9470×10227 | 12275×9555×9916 | 14730x 10860x 10341 | |
Main unit motor | Model | Y280M-6 | Y315M-6 | Y355M2-8 | Y3-355-4-8 |
Power(kw) | 55 | 90 | 160 | 280 | |
Rotate Speed(rmin) | 980 | 990 | 740 | 740 | |
Classifier speed regulating motor (variable frequency motor) | Model | Y132M-4 | Y180M-4 | Y200L-4 | YVP280M-4 |
Power(kw) | 7.5 | 18.5 | 30 | 90 | |
Rotate Speed(rmin) | 1440 | 1470 | 1470 | 1470 | |
Centrifugal induced draft fan motor | Model | Y250M-4 | Y315-4 | Y315L2-4 | Y315L2-4 |
Power(kw) | 55 | 110 | 200 | 315 | |
Rotate Speed(rmin) | 1480 | 1480 | 1480 | 1480 | |
Elevator | Bucket Model | TH210 | TH315 | TH315 | TB315 |
Motor Model | Y100L2-4 | Y112M-4 | Y112M-4 | Y160M-4 | |
Motor Power(kw) | 3 | 3 | 4 | 11 | |
Rotate Speed(rmin) | 1430 | 1430 | 1440 | 1440 | |
Jaw Crusher | Model | PE250×400 | PE250×750 | PE250×750 | PC1010 |
Motor Model | Y180L-6 | Y200L2-6 | Y200L2-6 | Y315M2-6 | |
Power(kw) | 15 | 22 | 22 | 110 | |
Rotate Speed(rmin) | 970 | 970 | 970 | 990 | |
Magnetic Vibrating Feeder | Model | GZ2F | GZ3F | GZ4F | GZ5F |
Power(kw) | 0.15 | 0.2 | 0.45 | 0.65 |
This product relates to wear easy wear of mechanical equipment in the village of high molecular chemical material field, in particular
Get Price And Support
Respond within 24 hours !
Simply complete the form below, click submit, you will get the price list and a SBM representative will contact you within one business day. Please also feel free to contact us by email or phone. ( * Denotes a required field).